top of page
Airplane Wing Optimization using Finite Element Analysis

Overview:
Given the specifications for a simplified wing geometry, this project requires optimizing the wing structure by modifying its geometry to minimize the weight. Simulations using ANSYS is critical to reach this goal and ensure structural integrity. The results must also be explained using a mathematical model. This project was done was a part of a finite element analysis course at Cornell University (MAE 4700: Finite Element Analysis for Mechanical and Aerospace Design).
Design Approach Using ANSYS:
Design goals: displacement < 0.375m; stress < 252 MPa; volume < 3m^3
1. Set up ANSYS model given the design constraints.
2. Begin by adding ribs, and check the effects on stress, displacement and volume.
3. Vary rib spacing, and check stress, displacement and volume again.
4. Continue design iterations by varying skin thicknesses, number of spars and thickness of spars.
Results:

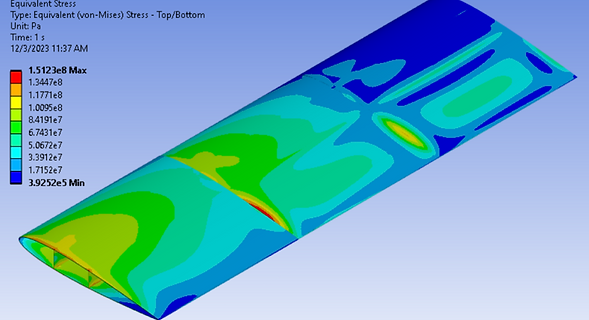
Displacement satisfied.
Stress satisfied.
Mathematical Model:
Based on Shell Theory: 3D system with 6 degrees of freedom per node.
The central assumption of shell theory is identical to that in Euler–Bernoulli beam theory: normals to the mid surface remain straight and normal. Since the shell theory derivations are quite involved, we will continue to analyze our model by making it analogous to beam theory.
Governing Equation:

Weak Form:

Essential Boundary Conditions:

Natural Boundary Conditions:
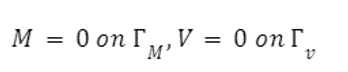
Report:
bottom of page